

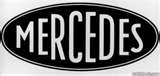


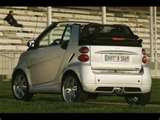
As a Mercedes-Benz technician at a prestigious company such as Crown Automobile, I would like to thank Mercedes-Benz, Bessemer State Technical College, and the rest of the people behind the star that I work with. I have been trained by Mercedes for Mercedes. This would not be possible without them. I am only one star in the constellation. I represent one of many who strive for excellence, and for continuing a reputation for uncompromising attention to detail and as always our goal is "Nothing but the best for our customers, let's do our best together!"
Attention! Next, I would like to say that the complicated process of applying for and obtaining official documentation. Stating, and I quote, "U.S. AND FOREIGN PATENTS APPLIED FOR


CONCEPT DESIGNED EXCLUSIVELY BY: DAVID NORTHCUTT aka Mbtech3@hotmail.com aka David_300sl@gmail. Mercedes Benz official licensed product ready! Direct the forces of rotational inertia with laser accurate control. This is the most efficient design possible. No expense spared for compromising quality and care in each and every thing we do!"
"If you like Benz and you love your babies... you should buy a Mercedes!!!" "
"Evolving ideas to empower the star in every person"
"Give yourself the very best life can offer by driving a Benz. It's always been the best by far."
"Energy efficiency of a smart car and mind bending acceleration of a Mclaren SLR!!"
"Give yourself the very best life can offer by driving a Benz. It's always been the best by far."
"Energy efficiency of a smart car and mind bending acceleration of a Mclaren SLR!!"
I am working on the heart of my invention, the Dynamic flywheel assembly first. I am planning to build the dynamic flywheel using 4 flywheels. The finished prototype of the dynamic flywheel will actually contain 2 counter rotating active mass assemblies. Energy is efficiently transferred to the Dynamic Flywheel rotors by a high performance coil arrangement similar to that of a brushless electric motor. Power storage of high magnitude can be stored in minimal space. This breakthrough in mass technology can direct inertial force exponentially with never before seen control. Super high speed active mass flywheels will allow gradual storage of high energy, and give the ability to deliver great amounts energy in the form of inertial thrust, torque, or electricity. Highly efficient, computerized control with a system of permanent magnets, brush less motors, coils, specialized speed and inertia thrust control, with a carbon fiber glass mat battery built into the rotating mass of the flywheel . The Dynamic flywheel uses a central processor, Lasers, photoelectric diode arrays, and Maglev technology to control dynamics of the active mass flywheel weights. Dynamic mass flywheel assembly will be connected by a center shaft with counter rotation by means of a light weight planetary gear set also of a special design. The rotating assembly will be supported by powerful neodymium magnetic bearings, mounted in a vacuum filled chamber. Virtually no friction will exist which results in minimal power loss. For safety purposes, a layered series of Kevlar webbing, and synthetic epoxy reinforced fiberglass will form a hull around the rotors. The active flywheels will be cased not only in a vacuum chamb
er but also incorporate a refrigerant system to further
improve conductivity of magnetic bearings, infa-red imaging, photoelectric diodes, and fiber optic lasers are used to control r.p.m's, directional inertia transmission, along with other on board systems such as navigation processor, turbine fans, and on-board camera and microphone arrays. I will describe these in due time, but it is a necessary and integral part of the design.The infared camera allows for monitoring thermal load spots, This allows for higher speeds and a on
board CPU for remote host PC control capability. Additionally, an board camera system necessary
to transmit streaming video for flight control via remote PC will be mounted to the flywheel casing or hull. I will use internal combustion engine flywheels and modify them as needed. MAGLEV rails, and cylinders containing motorized pistons of mass are in a radial arrangement in 2 flywheels, arranged in a pattern resembling wagon wheel spokes. The channels will be machined into
the flywheel so that when the two flywheels are mated together hollow cylinders will exist inside the assembly. 
Furthermore, closely spaced cylinders will accomo
date a floating cone shaped mass constructed of varying metals, high strength alloy layers, and permanent earth magnets that can be controlled actively inside both flywheels. To try to give an example arrange a series of separate 1 ounce weights in a perfect circle and imagine
these rotating at 20,000 rpm. Each of the weights (1 oz. weight represents the active mass piston) being attached to the center axis of rotation accelerated in a perfect circle until the desired speed is achieved. Now sequentially as each weight moves into the desired point of it's 360 degrees of travel allow it's own inertia to move to it's outer most position by reducing the electromagnetic field and rapidly pull it back in by increasing the electromagnetic field to it's original strength so that the path of each individual weight during the flywheels rotation would be shaped similar to the outline of the cross section of a camshaft lobe. As the weights are being pulled back in the force is achieved and can be varied by changing the deflection , dwe
ll angle, speed and number of the
rotating sequence of weights. Near the edges of the
flywheel the cylinders will start to get smaller and narrow into a point. The
purpose of the point is so that force can be directed into a smaller area with a high strength alloy bearing. I will add illustrations later to make some of this more clear. The movable weight mass I plan to construct in layers of metals to form a cone. then use small amount of le
ad then steel and so on with the higher strength metal alloys at the point which will bear most of the forces. Each movable weight will be controlled by variable electromagnetic pulses, the same way a bullet train is accelerated a
long a tra
ck. For controlling each mass cylinder a signal generator and op amp circuit with specific frequencies proportionate to flywheel speed will be used to control the in out movement of weights. As near as possible to the axis of rotation seperate control coils for each cylinder will allow for additional control for the weight inside the seperate cylinders. Incorporated in the design the gyrodrive cpu can allow any number of the weights to be controlled seperately during rotation and transmitted force output each mass cylinder weight continuously variable. Wi-Fi control of an on-board computer will allow control from your home or office. The on-board computer c
ontrols the sig
nal generator, which then controls
the
electromagnet coils on each of the cylinders. Once the dynamic flywheel is completed I will then attach a large hi performance Brush less electric drive turbine fans on top and bottom of the
counter-rotating dynamic flywheels. The turbine fans will provide cooling of the flywheel cpu and control coils. This assembly will be the heart of the dynamic flywheel, which I plan to use in conjuction with a second specialized system which incorporates an infinity shaped track with a continous train of dc motors with flywheels using sequential acceleration and braking of the rotors as they travel around the infinity track to produce lift or inertia control. Speed controlled gyroscopes mounted to an infinity shaped track controlled by an ecu could also be incorporated for use in aircraft to improve stability. I have also designed a gyroscopic device that could provide additional lift or stability for aircraft. I will explain further details and progresses in design later. I would just like to believe that we can always make advances in our technology. Leading the way, and driving me toward success, is Mercedes-Benz. I have dreams to discover big things. I believe I have the ability to design, build, and install the modifications necessary to drive my 300sl faster and farther that anyone else ever has. With all the safety and comfort in existence, stunning appeal and styling that makes a statement. I believe we can build a vehicle capable of travel anywhere on the planet, and possibly beyond from the comfort of my Mercedes-Benz 300sl! why not? No matter how short the resources we can make it up in sheer determination. I think it's possible.



























1. Energy chain as follows: Sunlight directed into a beam of light which is concentrated by magnifying glass onto 14k gold "energy antenna" made from a spherical mass of gold mounted on a conductive wire (conductive gold antenna and conductor will be cooled with a gas refrigerant heat exchanger circuit). The "gold conductor antenna will be equipped with a reflector of diode arrays to efficiently convert the sun's power to electrical power. Energy will be stored in capacitors, batteries, and dynamic flywheels Further enhancing performance is use of tiny infa red came

